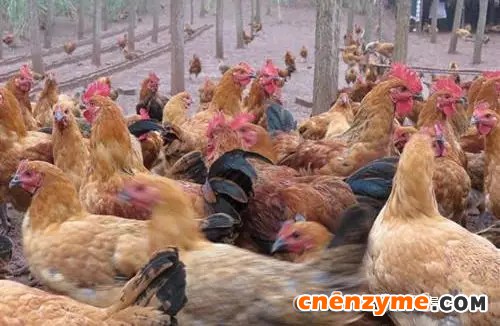
1材料与方法
1.1 试验设计
选用20日龄黄脚麻鸡180只,将肉鸡分为4组,每组5个重复,每个重复9只鸡,试验前称重。试验组1为对照组(基础饲粮中添加10%菌柄),试验组2为基础饲粮中添加10%普通发酵饲料(仅添加益生菌剂发酵),试验组3为基础饲粮中添加10%FAE酶化饲料(仅添加FAE酶化),试验组4为基础饲粮中添加10%酶化发酵饲料(添加益生菌剂发酵及FAE酶化)。
采用地面平养方式饲养,全天光照,每天饲喂3次,自由采食、饮水,定时对鸡舍进行消毒清扫(每周2次),试验时间为25d,按正常肉鸡免疫程序进行免疫。肉鸡基础饲粮标准参照NY/T33-2004《鸡饲养标准》中肉鸡营养需要配制,其组成及营养水平见表1。
1.2 试验材料
1.2.1 主要器材
反式阿魏酸标准品(美国某公司);阿魏酸甲酯(华侨大学曾庆友老师合成);XOS标准品、木二糖标准品(日本某公司);超滤膜包Vivaflow200(MWCO 30KD)(北京某公司);发酵袋(郑州某公司)。1100高效液相色谱仪(美国某公司);HPX-42A柱(美国某公司);ODS-C18色谱柱(美国某公司);SP-2102UV紫外可见分光光度计(上海某公司);凝胶成像系统GIS-2008(上海某公司)。
1.2.2 饲料原料
玉米蛋白粉(山东某饲料厂);瓜尔豆粕(广饶某公司);棕榈仁粕(大连某公司);预混料(厦门某公司);益生菌剂(1.0×1010CFU/g)(山东某公司);杏鲍菇菌柄(福建某公司)。
1.2.3 鸡苗
黄脚麻鸡(厦门某种禽厂)。
1.2.4 试验地点和时间
厦门市集美区仙灵旗农庄,试验时间为2013年4-5月。
1.3 饲料发酵方法
1.3.1 FAE粗酶液的制备
1.3.1.1 菌种
黑曲霉,实验室自行筛选并保藏。
1.3.1.2 培养基成分
种子培养基:PDA培养基,36℃,200r/min培养2d。发酵培养基:麦糟及麦麸干燥粉碎过100目筛,麦糟∶麦麸=1∶4(m/m)比例加入白瓷盘中并按1∶1.5(m/V)添加营养盐溶液,混匀,121℃灭菌30min,33℃培养6d。营养盐溶液:蛋白胨0.2%,酵母粉0.4%,NaH2PO4·2H2O 0.152%,KH2PO4 0.1%,CaCl2 0.03%,MgSO4·7H2O 0.03%,Na2HPO4·12H2O 3.14g,Na2HPO4·2H2O 1.56%。
1.3.1.3 粗酶液的制备
发酵料中加入8倍体积的蒸馏水,33℃,180r/min中抽提2.5h,静置,用8层纱布过滤,得滤液,再将滤液超滤制备得FAE粗酶液,FAE粗酶液酶活达20U/mL以上。超滤条件为操作温度20℃、压力0.1MPa及进料速度200mL/min。
1.3.2 普通发酵饲料及酶化发酵饲料的制备
发酵培养基(以干物质计):菌柄12%,玉米蛋白26%,棕榈仁粕11%,谷壳粉16%,瓜尔豆粕5%,玉米粉5%,糖蜜0.3%。
普通发酵饲料制备:将发酵培养基加入0.1%益生菌剂混合均匀,装入发酵袋常温发酵。每袋质量为1000 g。
酶化发酵饲料制备:按8U/g 干菌柄将FAE粗酶液加入到发酵培养基中,再加入0.1% 益生菌剂混合均匀,装入发酵袋常温发酵。每袋质量为1000 g。
1.4 指标测定与方法
1.4.1 饲料常规成分测定
粗蛋白质含量按GBT6432—1994《饲料中粗蛋白质测定方法》分析;中性洗涤纤维(neutraldetergentfiber,NDF)含量按GB/T20806—2006《饲料中中性洗涤纤维的测定》分析;酸性洗涤纤维(aciddetergentfiber,ADF)含量按NY/T1459—2007《饲料中酸性洗涤纤维的测定》分析;酸性洗涤木质素(aciddetergentlignin,ADL)含量按GB/T20805—2006《饲料中酸性洗涤木质素的测定》分析。
1.4.2 总氨基酸、乳酸含量测定
总氨基酸含量采用南京建成生物工程研究所的总氨基酸测定试剂盒,原理为铜离子(Cu2+)与氨基酸的显色反应。乳酸含量采用南京建成生物工程研究所的乳酸测试盒测定,原理为乳酸脱氢酶的显色反应。
1.4.3 总菌数、乳酸菌数测定
总菌数按GB/T13093—2006《饲料中细菌总数的测定》分析。乳酸菌数按GB4789.35—2010《食品安全国家标准食品微生物学检验乳酸菌检验》分析。
1.4.4 饲料发酵前后小分子肽变化测定
采用不连续凝胶电泳分析。上层丙烯酰胺5%,下层丙烯酰胺15%。
1.4.5 XOS和FA含量测定
XOS含量采用HPLC测定。HPX-87H色谱柱,示差折光检测器。柱温50℃,流动相5mmol/L的硫酸,流速0.4mL/min。FA含量采用HPLC法测定。色谱柱为ODS-C18柱,318nm检测,柱温30℃。流动相为甲醇∶水∶冰醋酸=30∶69.5∶0.5(V/V/V),流速为0.9mL/min。
1.4.6 饲料卫生指标检测
饲料送至福建省分析检测中心,按GB13078—2001《饲料卫生标准》分析。
1.4.7 肉鸡鸡肉品质
肉鸡送至福建省分析检测中心,按GB18406.3—2001《农产品安全质量无公害畜禽安全要求》分析。
1.5数据统计
分析数据采用SPSS19.0软件的ANOVA进行方差分析,Duncan氏法进行多重比较,各组数据以平均值±标准差(mean±SD)表示。
2结果与分析
2.1 发酵过程中影响饲料品质的因素变化
2.1.1 发酵过程中饲料重量变化
由表2可知,发酵过程中2个试验组饲料重量都呈下降趋势,第0天与第15天饲料重量差异显著(P<0.05),随着发酵进行,酶化发酵饲料重量减少比普通发酵饲料多,说明酶化发酵饲料代谢较彻底。发酵过程中饲料重量的减少是由于发酵基料水分的挥发、发酵过程中微生物的活动及酶促反应,使基料中的碳水化合物及蛋白质等大分子有机物分解成小分子物质而损失。
2.1.2 发酵过程中FA含量变化
由表3可知,在整个发酵过程中普通发酵饲料FA含量在0.23~0.40mg/g,变化范围小;而酶化发酵饲料随着发酵时间的延长,FA含量迅速上升,第10天FA含量达最高,为4.11mg/g,与第0天比,差异极显著(P<0.01)。这是因为在酶化发酵饲料中加入了FAE,FAE与益生菌产生的木聚糖酶协同作用释放出FA;而普通发酵饲料因没有添加FAE,发酵过程中FA含量很低。
2.1.3 发酵过程中XOS含量变化
由表4可知,2个试验组发酵开始,XOS含量都是随着发酵时间增加而增加,但酶化发酵饲料XOS含量明显比普通发酵饲料高,这是由于酶化发酵饲料添加的FAE与益生菌产生的木聚糖酶协同作用,提高了XOS的含量。发酵第10天,酶化发酵饲料其XOS含量达最高,为36.33mg/g,与第0天比,差异显著(P<0.05);而普通发酵饲料第9天达最高,为20.43mg/g,与第0天比,差异显著(P<0.05),随后2个试验组XOS含量都缓慢下降。
2.1.4 发酵过程中粗蛋白质含量变化
由表5可知,在整个发酵过程中,酶化发酵饲料的粗蛋白质含量高于普通发酵饲料。这是因为FAE的加入,增加饲料中XOS的量,而XOS有利于益生菌剂中乳酸菌、枯草芽孢杆菌、酵母菌的繁殖,从而提高了酶化发酵饲料中粗蛋白质的含量。发酵第5天,酶化发酵饲料及普通发酵饲料粗蛋白质含量都达最高,酶化发酵饲料粗蛋白质含量到达24.67%,与第0天比,差异极显著(P<0.01);而普通发酵饲料最高为23.15%,与第0天比,差异显著(P<0.05),随后粗蛋白质含量都缓慢下降。试验结果与胡瑞等研究酶菌联合发酵对豆粕品质影响时,粗蛋白质含量变化结果一致。
2.1.5 发酵过程中总氨基酸含量变化
由表6可知,在整个发酵过程中,酶化发酵饲料总氨基酸含量都高于普通发酵饲料。发酵开始,2个试验组中总氨基酸含量都随着发酵时间增加而增加,第8天酶化发酵饲料及普通发酵饲料总氨基酸含量都达最高,分别为21.26、13.29mg/g,与第0天比,差异显著或极显著(P<0.05或P<0.01),随后总氨基酸含量逐渐下降。与李龙等利用复合益生菌发酵饲料时,总氨基酸的变化趋势一致。
2.1.6 发酵过程中总菌数变化
如表7可知,在发酵开始阶段,由于饲料中营养丰富,2个试验组总菌数都是呈上升趋势,第10天酶化发酵饲料总菌数为22.00×105个/g,与第0天比,差异显著(P<0.05),第9天普通发酵饲料总菌数为10.00×105个/g,与第0天比,差异显著(P<0.05);随后,乳酸的生成使得饲料中pH降低,导致饲料中有些菌不适应环境而数量开始减少;发酵后期总菌数保持稳定,这与贾鹏辉等试验结果相类似。酶化发酵饲料可能由于FAE作用,产生较多XOS,促进益生菌大量增殖而总菌数较普通发酵饲料多。
2.1.7 发酵过程中乳酸菌数变化
如表8可知,发酵开始,酶化发酵饲料及普通发酵饲料乳酸菌数都是呈上升趋势,在第12天其菌数都达最大,其乳酸菌数分别为9.300×105及3.200×105个/g,与第0天比,差异都显著(P<0.05)。之后由于乳酸菌处于衰亡期,2个试验组的乳酸菌数开始下降并趋于平衡。
2.1.8 发酵过程中乳酸含量变化
从表9可知,整个发酵过程2个试验组乳酸含量一直增加,在第10天,酶化发酵饲料乳酸含量达最大,为8.79g/kg,与第0天比,差异显著(P<0.05);普通发酵饲料在第9天达最大,为7.14g/kg,与第0天比,差异显著(P<0.05)。经过一定时间发酵后,乳酸菌增殖减缓,分泌的乳酸减少,乳酸含量维持在一定水平。乳酸含量增加会提高饲料的适口性,对动物的生长有积极的促进作用。
2.1.9 发酵过程中饲料pH变化
由表10可知,发酵第1天,2个试验组pH基本一致,第3天后,由于乳酸菌的繁殖,导致pH下降,由于酶化发酵饲料乳酸菌较普通发酵饲料多,使得酶化发酵饲料的pH较低。发酵第15天,酶化发酵饲料的pH为4.25,普通发酵饲料的pH为4.32,与第0天比,差异都极显著(P<0.01)。
2.1.10 发酵过程中ADF、ADL、NDF含量变化趋势
由表11可知,酶化发酵饲料中ADL、ADF和NDF含量都比普通发酵饲料要低,且第10天2种发酵饲料ADL、ADF和NDF含量与第0天比都差异显著或极显著(P<0.05或P<0.01)。这是因为酶化发酵饲料中FAE与益生菌剂中微生物分泌的非淀粉降解酶协同降解发酵原料中的木质纤维,提高了木质纤维的降解率,因此酶化发酵饲料在降低饲料中抗营养因子的同时还能提高饲料中的营养成分。
2.1.11 发酵过程饲料中小分子肽变化
图1可知,随着发酵时间进行,普通发酵饲料与酶化发酵饲料中大分子蛋白质能够降解为小分子肽,这是因为发酵饲料中有益菌的生长产生了更多的蛋白质水解酶,促进了小分子肽含量的增加。肽更容易被动物吸收,提高饲料品质。
2.1.12 饲料卫生指标检测
经检测,酶化发酵饲料的各项卫生指标符合GB13078—2001《饲料卫生标准》要求。
2.2 发酵饲料对肉鸡生产性能的影响
2.2.1 发酵饲料对肉鸡成活率的影响
将不同的发酵饲料以10%的比例添加到肉鸡基础饲粮中,肉鸡饲养结果如表12。在饲喂全程中,饲粮中未添加任何的抗生素及其他的药物,各组鸡的死亡率均为0,死亡率差异不显著(P>0.05),并未体现出添加发酵饲料抗病的优势,这可能与饲养管理合理,场地卫生条件好有关。
2.2.2 发酵饲料对肉鸡生产性能的影响
从表13可知,与对照组相比,FAE酶化饲料和酶化发酵饲料均能提高肉鸡平均日增重,分别提高了1.23%、4.31%,而普通发酵饲料则使肉鸡平均日增重降低了1.98%,但是差异不显著(P>0.05)。发酵饲料能提高平均日增重,这与发酵饲料中含有更多的营养物质且肉鸡养分利用率的提高有关。普通发酵饲料、FAE酶化饲料和酶化发酵饲料均有降低平均日采食量的趋势,分别降低了2.58%、3.01%、8.34%,但是差异不显著(P>0.05)。酶化发酵饲料对降低料重比具有极显著的作用(P<0.01),降低了12.45%,虽然普通发酵饲料和FAE酶化饲料也能降低料重比,但是只分别降低1.24%和8.30%(P>0.05)。酶化发酵饲料与普通发酵饲料相比,肉鸡平均日增重提高了6.42%(P>0.05),平均日采食量降低了5.91%(P>0.05),料重比降低了11.34%(P>0.05)。而本课题组的杨道秀等将FAE粗酶液及商品饲料酶-“溢多酶”(主要含木聚糖酶、纤维素酶、淀粉酶等)添加入饲料中,试制酶化饲料饲喂肉鸡,与对照组相比,肉鸡平均日增重提高了4.37%,料重比降低了7.63%,与本试验结果相近。
2.2.3 肉鸡卫生检测指标结果
鸡肉各项卫生指标符合GB18406.3—2001《农产品安全质量-无公害畜禽安全要求》。
3讨 论
厦漳食用菌的生产规模位居全国之首,在生产过种中,产生了大量的菌柄下脚料。菌柄营养非常的丰富,如杏鲍菇的菌柄,经本课题组测定,粗蛋白质含量为12.53%(干重),多糖含量为33.74%(干重),游离氨基酸含量为3.56%(干重)。但其非淀粉多糖抗营养因子高,直接饲喂动物适口性差。因此试验选用杏鲍菇菌作为主要的发酵原料。
目前已有FAE对反刍动物饲料中提高木质纤维降解率的报导,杨红建等申请专利《一种饲用复合阿魏酸酯酶添加剂》,表明饲料原料中添加FAE可提高牧草、农作物秸秆及糠麸类饲料酶解过程中还原糖释放量、细胞壁降解率以及瘤胃发酵挥发性脂肪酸的产生量。Krueher等在百喜草、百慕达草中添加不同浓度的FAE酶液,结果发现瘤胃微生物对NDP的降解有显著的促进作用,降解程度与酶的添加量成线性关系。这些报导关注的都是阿魏酸酯酶对饲料中非淀粉多糖降解率的影响,未涉及酶与木质纤维降解产物(如阿魏酸及低聚糖)的关系及降解产物对动物的影响。本文研究结果表明添加了FAE的发酵饲料,不仅提高了饲料中的ADF、NDF及ADL降解率,且产生了对动物有生理活性的FA及XOS,饲喂肉鸡时,有利于降低料重比。
4小 论
①酶化发酵饲料与普通发酵饲料相比,其产生的XOS和FA更多,酶化发酵饲料FA含量最高为4.11mg/g,其XOS含量最高为36.33mg/g。
②酶化发酵饲料与普通发酵饲料相比,饲料中粗蛋白质含量、总氨基酸含量、总菌数及乳酸菌数都更高,且其ADF、NDF及ADL在发酵过程中得到更好的降解。
③酶化发酵饲料与普通发酵饲料相比,肉鸡平均日增重提高了6.42%,平均日采食量降低了5.91%,料重比降低了11.34%,而肉鸡饲粮中添加普通发酵饲料和FAE酶化饲料均能够促进肉鸡的生长,但效果不显著。